Ansys 2022R1 Released!
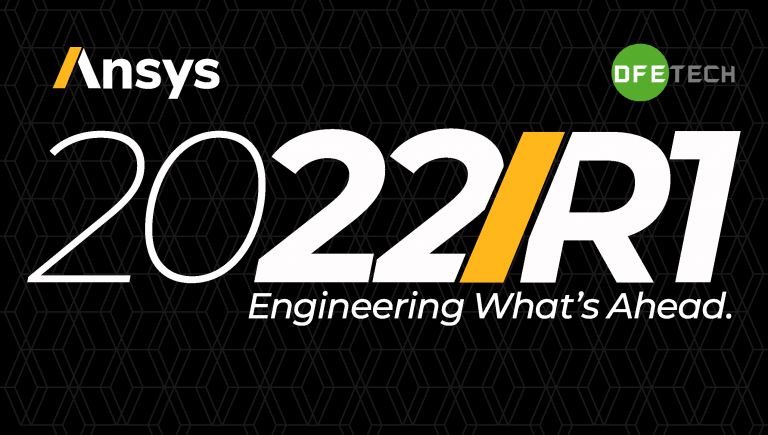
Across the entire portfolio of the Ansys family of programs, a couple of features have been added in Ansys 2022 R1 to help engineers optimally develop the products of tomorrow. With the newly launched Ansys 2022 R1, engineers can capitalize on ever-increasing computing power to optimize complex products, assemblies and systems across industries; and bring better products to market faster with systems engineering workflows that bring together multiple engineering tools and disciplines to help stakeholders understand subsystem interactions and synergies. With access to nearly limitless computing via Ansys Cloud, engineers who use Ansys 2022 R1 products have the speed and flexibility to ask the “what-if” questions that lead to innovations in autonomous vehicles, chip design, mission-critical connectivity solutions and more sustainable travel via lightweight materials and electrification, thus engineers are no longer bound to an expensive and time-consuming prototype-test-redesign cycle.
Buttons below will bring you to ANSYS 2022R1 updates session in different Ansys product families:
STRUCTURAL
2022 R1 introduces a new product, Ansys Forming. Ansys Forming is an all-in-one forming simulation software built to digitally design and validate every step of the sheet metal forming process leveraging the speed and accuracy from the LS-DYNA solver.
- Increased confidence in correlating test and simulation data with the new noise, vibration, and harshness (NVH) toolkit inside Ansys Mechanical. Users can easily read physical test data and compute the modal assurance criteria (MAC) to compare simulation data and physical test data
- Additional insights into PCB thermal performance with high-fidelity PCB models from Sherlock that can now be exported to Ansys AEDT Icepak for thermal analysis simulations
- LS-DYNA solver continues to add exciting new features in many areas like dedicated isogeometric analysis (IGA), advanced new materials, and material laws for multiphysics applications, which can be used for battery-abuse modeling, electrophysiology, and many more areas
ANSYS MECHANICAL
- Better utilization and performance with the hybrid parallel technique within the Mechanical solver. This new technique provides more flexibility and efficiency by pushing the limits of user’s hardware, memory and simulation environment to get the most efficient runs out of a user’s available resources
- Increased confidence in correlating test and simulation data with the new NVH (Noise Vibration Harshness) toolkit inside Mechanical. Easily read in physical test data and compute the MAC (Modal Assurance Criteria) to see how well the test data matches the physical test
- Condense elements into one “super element” with substructure generation analysis that enables users to represent their model with ROMs (reduced order models) which saves simulation time and encourages sharing models across engineering groups
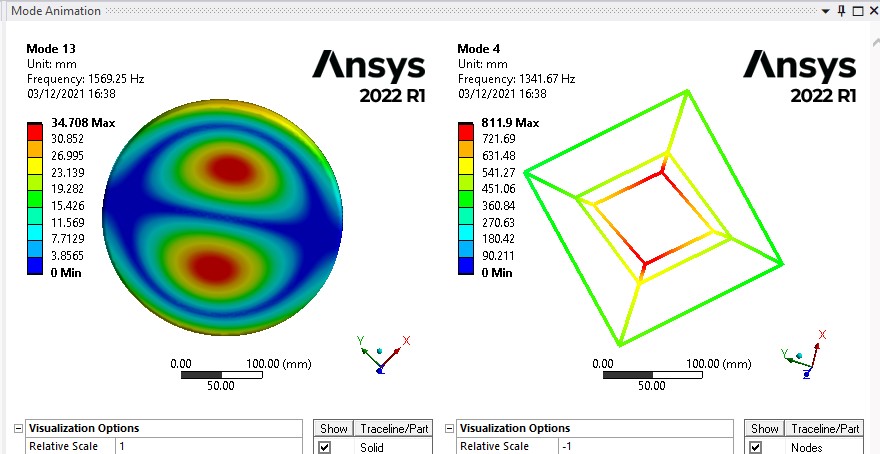
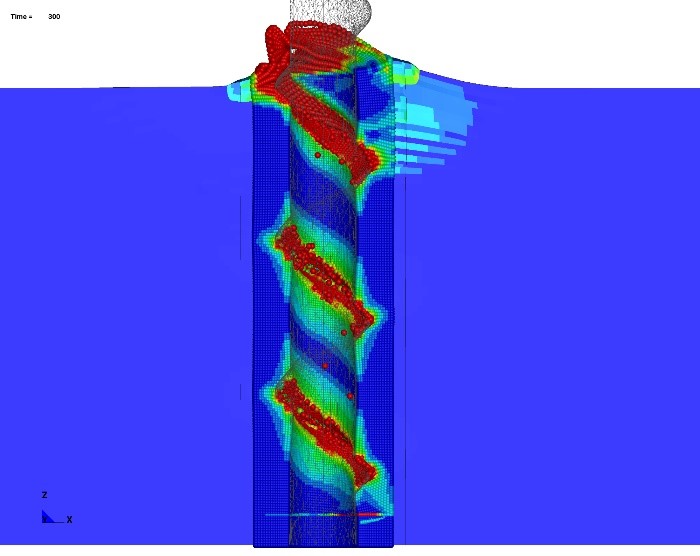
Ansys LS-DYNA
- Continued integration of LS-DYNA technologies in Mechanical to run LS-DYNA simulations more efficiently with improvements in Restart capabilities such as change in Boundary Condition support, and the modification of imposed displacements
- LS-DYNA solver continues to add exciting new features in many areas like dedicated Iso-geometric Analysis (IGA) cards, advanced new materials, and material laws for multi-physics applications, which can be used for battery-abuse modeling, electro-physiology, and many more areas
- New improvements to Smooth Particle Galerkin (SPG) enables users to achieve more accurate and fast solutions
Ansys Motion
- Continued work to integrate Motion into Ansys ecosystem and 3rd party tools, such as FTire. This connection help users to acquire tire data and run their vehicle dynamics jobs directly in Motion
- Continued Motion integration into Mechanical – stresses, and strains can now be evaluated in Mechanical at element nodes to improve result accuracy
- Solver performance improvement, up to 50% speed improvement for certain models
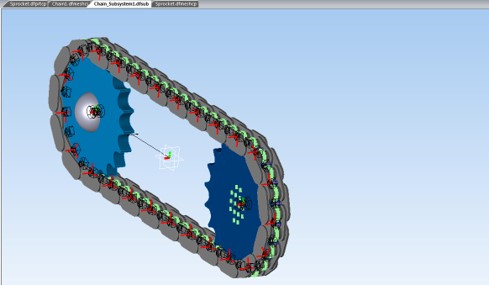
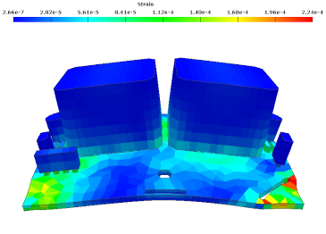
Electronics Reliability
- Additional insights into PCB thermal performance with high-fidelity PCB models from Sherlock that can now be exported to Ansys AEDT Icepak for thermal analysis simulations
- New semi-automated Reinforcement Technology workflow automates many previously manual tasks in Sherlock, such as the assignment of reinforcement material, thickness, and type properties for traces and vias
- New GDSII/EDB file import capability allows users to import chip- and die-level models directly into Sherlock as a part of their pre-processing workflow
Ansys Forming
Ansys Forming enables early stage and detailed design configurations by allowing users to preset varying simulation needs, including feasibility, formability and springback prediction. Through this end-to-end workflow, engineers can perform the entire die process on a single platform, eliminate the need for physical testing, and enhance productivity and cost savings. Ansys Forming reaches optimum performance by maintaining accuracy and speed.
- Simulates metal stamping tasks through an end-to-end workflow that allows you to perform the entire die process in a single platform, easy to use GUI, with the fastest solve time
- Achieve optimal performance, maintain speed and accuracy, and enhance your productivity and cost savings by reducing die cuts and redesign. Highly scalable SMP and MPP performance with LS-DYNA as a solver for metal stamping
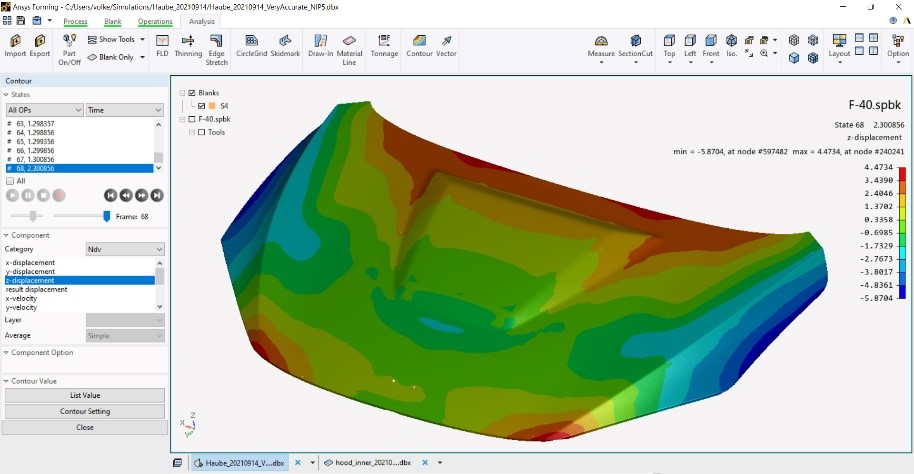
- Significantly reduce the number of elements during simulation and speed up solve time with smart adaptivity capabilities for users to accurately refine the mesh
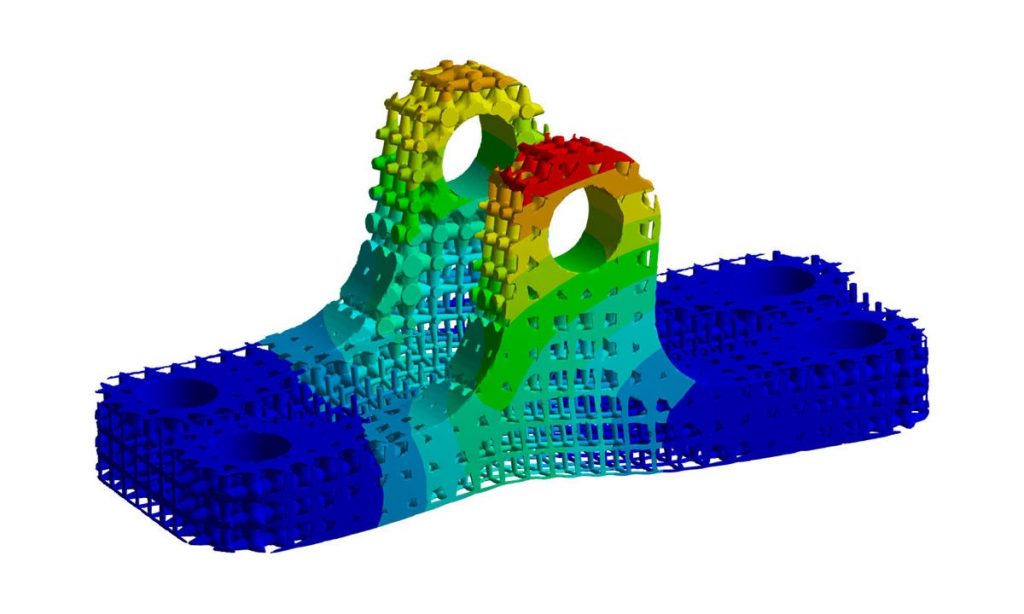
Ansys Additive
Ansys 2022 R1 continues to expand toolsets for Additive Manufacturing Users, streamlining your workflows between design, simulation, and manufacturing. In addition, every Ansys Mechanical User can now identify and minimize risk for build errors and ensure high-quality parts through process simulation for metal powder bed fusion (PBF), directed energy deposition (DED), and metal binder jetting.
- Streamline your workflows with directed energy deposition (DED) – introducing DED process simulation to the Ansys Additive Portfolio, providing capabilities from predicting macro-level temperature distortions and stresses to prevent build failures and provide trend data for improving designs for additive manufacturing including part orientation and part build order
- Continued improvements for power bed fusion (PBF) process simulation – double the strain generation speed for scan pattern simulations, paired with an expanding material library
- Workflow speed improvements – fully threaded solver support, multi-platform additive wizard support, Ansys Mechanical parametric design language (MAPDL) solver enhancements, and now providing a seamless transfer from Ansys Additive Products to Ansys Workbench and Ansys Mechanical
Ansys VRXPERIENCE Sound
For 2022 R1, Ansys VRXperience Sound will be officially renamed to Ansys Sound. For this release, the focus is around improved sound quality and design for our users, including:
- Optimize acoustic performance and reduce noise annoyance with tonality indicators that can be calculated in display order with the ability to switch order levels. This is especially of interest to customers working with rotating machinery
- A color map display for the ISO 532-1 standard so users can immediately check the time (or RPM) and frequency to ultimately reduce noise annoyance
- Fully released FRF (Frequency Response Function) capability allows users to characterize the transfer function of a system by estimating frequency response and minimizing the effect of noise at the receiver. Results can be transferred to Fluent to filter a simulation result for a more robust analysis
All information has been prepared to the best of our knowledge. Data without guarantee.
MATERIALS
2022 R1 sees Ansys Materials expand its data and tools offering into the 5G, electronics and electrification technology areas – extending Ansys Material Intelligence to Ansys Electromagnetic Simulation.
For the first time Ansys Granta MI™ will incorporate Machine Learning capabilities for intelligent additive manufacturing. Optimize the relevant parameters to meet your target criteria to reduce sample manufacture and characterization of additive materials previously done by trial and error.
- EMI/EMC, Electric Machine, SI/PI and Thermal engineers using Ansys Electronics Desktop tools can now access Granta MI in their native solvers – with access to a new range of 7,200+ electromagnetic material records. For faster, more accurate and traceable electromagnetic design simulation
- The volume of data for additive manufacturing continues to grow. To harness this trend Machine Learning capabilities have been integrated into Granta MI™ for process parameter optimization, data visualization and training. Bringing value to sparse and noisy additive data
- Assess a material’s environmental impact by using the comprehensive sustainability data in the unique Material Universe™ – updated with the latest ecoinvent data for all engineering materials
- Significant enhancement in our range of polymer data for non-linear material models – now with over 105,000 polymers
ELECTRONICS
The Ansys Electronics solutions 2022 R1 release continue to bring best-in-class technologies to address PCB, 3D IC package, EMI/EMC, thermal, cabling, and electromechanical design challenges with significant advancements in 5G, autonomous and electrification simulation. The new release features summary is as below:
- Phi-plus Technology now directly integrated into HFSS Mesh Fusion Workflow
- Automotive Radar Surface Roughness Model in HFSS
- Poly-Phase Electrical Machine ROM and Litz Wire Loss Prediction Ability with Temperature Feedback in Maxwell
- SIwave can read temperature gradients from Icepak and can automatically generate HFSS Regions in HFSS 3D Layout
- 2-way CPS workflow in AEDT Icepak and Enhanced Electro-Thermal-Structural workflows
- Multi-physics simulation and NVH Analysis using Motor-CAD
- EMA3D and Nexxim Transient Circuit Co-Simulation
- EMA3D Charge with dielectric breakdown capability
- Automated discrete optimization in Nuhertz FilterSolutions
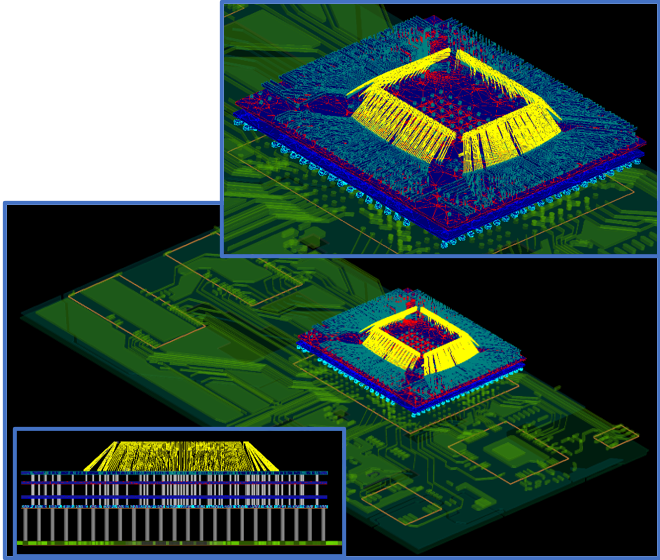
Ansys HFSS
- Phi-plus technology is now fully integrated into the HFSS Mesh Fusion technology which allows HFSS users to solve complex and large-scale designs. Phi Plus meshing technology brought a significant breakthrough in speed and capacity for 3D IC package challenges, especially with wire bonds
- HFSS SBR+ automotive radar surface roughness model provides an efficient method for modeling rough surface non-specular reflection, boosting the realism of radar simulation outputs
- Broadband Fast Sweep provides faster solutions with a less computational effort by requiring fewer solved basis points to deliver broadband simulation outputs
Ansys Maxwell
- New Poly-Phase Electrical Machine ROM helps to evaluate the entire drive system including power electronics with flexibility, greater accuracy, convenience, and using less computational effort
- Litz Wire loss prediction ability from two-way thermal coupling with thermal solvers in Workbench and Ansys Electronics Desktop. A new capability for designing Magnetic components of any power electronic configuration
- System push-back excitation for 2D/3D magnetic transient provides a faster alternative to simulate designs such as electric drive systems with detailed FEA analysis, reducing the total computing time drastically
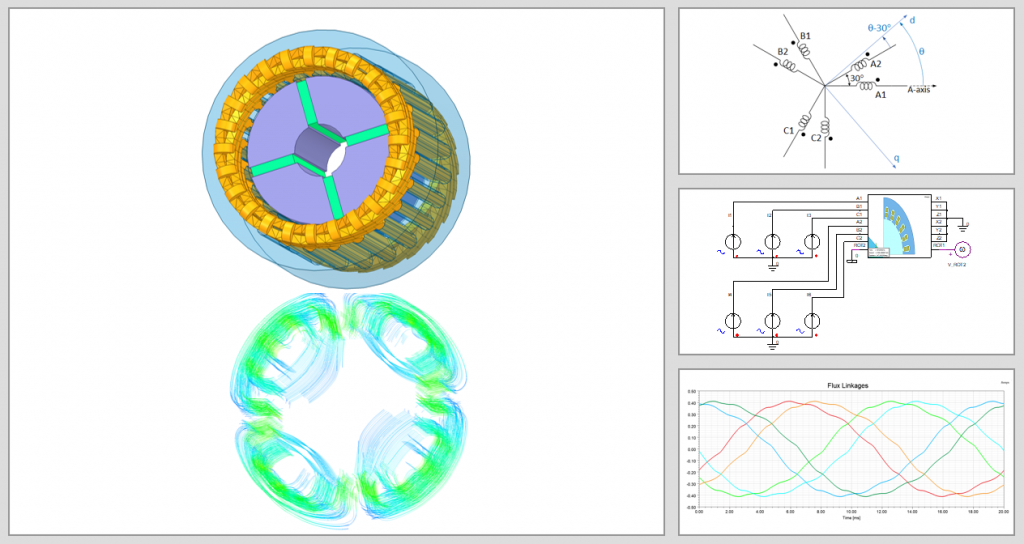
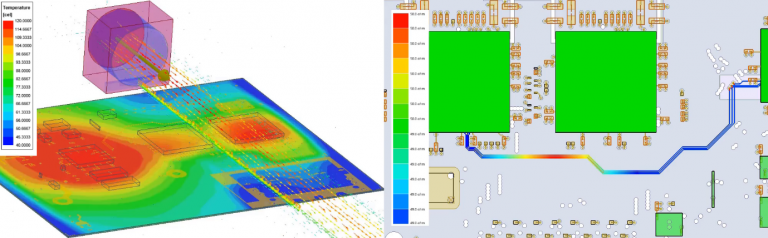
Ansys SIwave
- SIwave can read temperature gradients from Icepak and becomes the first in the industry to run AC simulations such as SYZ extraction and impedance and crosstalk scanners. This allows engineers to understand the temperature effects on the Signal Integrity of their designs
- SIwave can automatically generate HFSS Regions when using SIwave solver in HFSS 3D Layout. The regions are automatically created and can be modified by the user as desired. This automation speeds up the creation of the HFSS regions by orders of magnitude
Ansys Icepak & Mechanical in AEDT
- Icepak now allows for a 2-way link between RedHawk for CTM import and HTC export for a more accurate chip/package thermal solution
- Ansys Icepak trace-mapping can now be imported into Ansys Fluent using a new PCB model to perform advanced electronics cooling analyses that can include condensation, evaporation and more
- Mechanical Structural designs now link to Mechanical Thermal solutions in addition to Icepak for full Electro-Thermal-Mechanical Multiphysics solutions
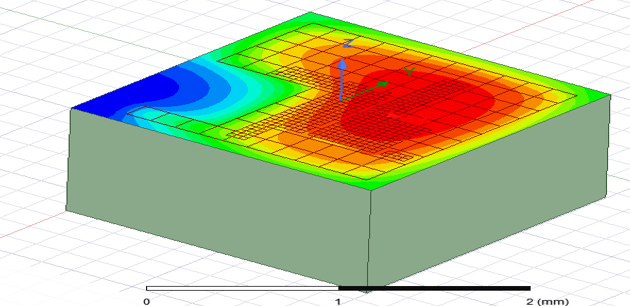
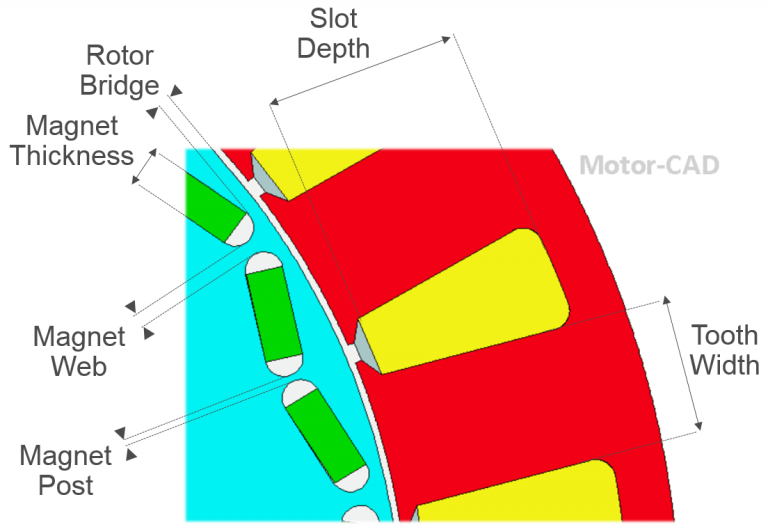
Ansys Motor-CAD
- Multi-physics optimization workflows using Motor-CAD and optiSLang can be set-up with a powerful new electric machine requirements and objectives interface
- The NVH of an electric machine can now be rapidly evaluated and assessed in the early stages of design and included as part of the multi-physics evaluation of a candidate design with Motor-CAD
- New seamless model export from Motor-CAD to Ansys Discovery enables the utilization of the Ansys Fluids and Structural solvers during the electric machine design process
Ansys EMA3D Cable
- EMA3D and Nexxim transient circuit co-simulation ability can simulate the complexity of devices and platforms down to the circuit level and reduce the simulation time by more than a factor of ten
- New material property and cable libraries accelerate the making and sharing of complex full vehicle models
- Expanded cable harness connectivity features allow EMC, E3, and RF Engineers to model real-world scenarios while designing cables for automotive, aerospace, and device manufacturing with ease, more accuracy, and lesser time
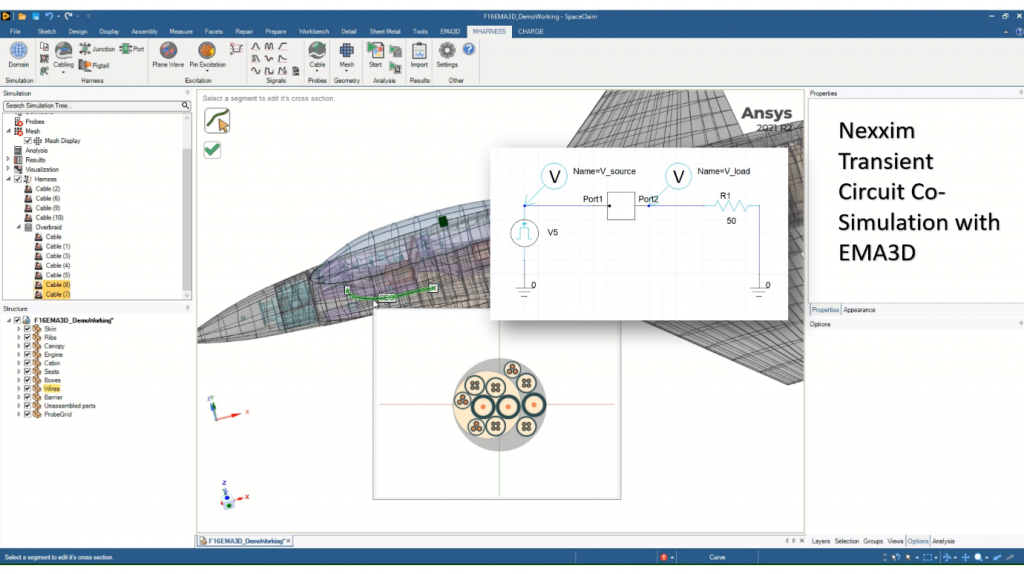
Ansys EMA3D Charge
- EMA3D charge is a new modeling solution of charging, discharging, and charge carrier transport across a wide range of applications, in one streamlined workflow. It is used by aerospace companies to simulate surface charging due to radiation. It is also capable to simulate electrical arc, non-contact ESD, and dielectric breakdown
- New dielectric breakdown capability will evaluate designs with risk of dielectric breakdown and assess the risk of dielectric breakdown between PCB traces
- Availability of structured extrusion mesh will significantly reduce computational time by refining mesh resolution in relevant regions
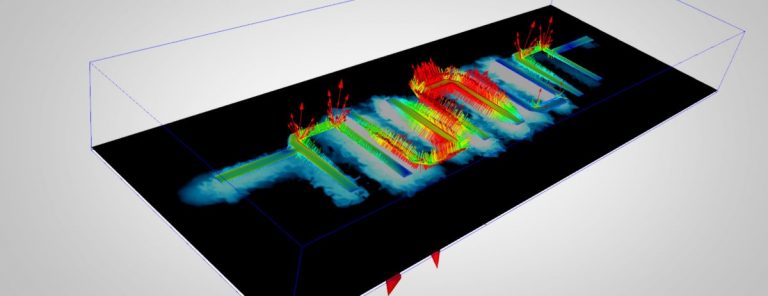
All information has been prepared to the best of our knowledge. Data without guarantee.
Ansys Nurherts Filter Solutions
- Automated discrete optimization can synthesize, optimize and simulate yield analysis of planar filter designs across standard value components available from vendors
- Support discrete element component models from Modelithics in Nuhertz filter synthesis. Modelithics provides accurate, measurement-based surface mount component models that enhance high-Q discrete component circuit designs at multi-GHz frequencies
3D DESIGN
Ansys 2022 R1 expands Discovery’s astonishing Live physics in the critical area of thermal management through the addition of coupled fluid-solid simulation.
This fast, fault-tolerant approach means that the simulation of heat exchangers, liquid cooling devices, and exhaust systems is now dramatically easier to perform and up to 50x faster allowing testing of more design variations for expanded insight and discovery. Enhancements include:
- Fast and easy thermal management–Coupled fluid-solid thermal analysis for Live physicsallows fast prediction of heat dissipation and transfer under many fluid flow scenarios
- Geometry preprocessing –Support for beams and shells, flex cable wrapping, and small units make Discovery a compelling tool for working with a wide range of geometries and use cases
- Workflow Innovation –Expanded history tracking, improved hinge and spherical joints, as well as newpostprocessing capabilities, such as local slice monitors and interactive probes, accelerate the simulation journey from setup to results
- Additional physics –Compressible flow for both Live and High-fidelity physics, temperature-dependent material properties, and 1D springs expand the scope and depth of Discovery’s simulation capabilities
FLUID
The new release features major enhancements in the Fluids portfolio that accelerate meshing, setup, and solve time. This release is enabling engineers to innovate to new levels in applications involving electrification, turbomachinery, aerospace and more, with transformational new features that include:
- An aerospace-dedicated workspace in Ansys Fluent streamlines external aerodynamics simulations with built-in best practices, optimized solver settings, parametric capabilities, and more
- A brand-new Multi-GPU Fluent solver (beta) accelerates steady-state simulations, with results showing 4 high-end GPUs provide the same performance as more than 1,000 CPUs
- Efficiently run acoustics simulations in Ansys Fluent with the new sponge layer treatment and perform sophisticated analyses with sound composition and runtime Discrete Fourier Transform (DFT) framework
- Ansys TurboGrid’s hybrid meshing technology automates the meshing of complex turbomachinery blade designs
- Accelerate Ansys Rocky simulations by reducing computation in regions with low particle interaction using a dynamic domain capability
- Ansys Forte’s Eulerian two-phase mixture approach to modeling liquids and two-phase mixtures enables quick and accurate simulation of liquid pumps and valves
Ansys Fluent
- An aerospace dedicated workspace tailors the user interface to external aerodynamics simulations and streamlines the workflow with built-in atmospheric conditions, optimized solver settings, relevant input and output parameters and more
- A brand-new Multi-GPU Fluent solver (beta) accelerates steady-state CFD simulations, with results showing 4 high-end GPUs provide the same performance as more than 1,000 CPUs. Cost savings can be seen with a 4X reduction in power consumption and consistent hardware savings as well
- Solve acoustics simulations more efficiently with a new sponge layer option that reduces setup and solve time and the ability to compose audio signals and transfer files to Ansys Sound directly from the Fluent interface
- Efficiently evaluate the Discrete Fourier Transform (DFT) of any variable in the entire domain with a new runtime framework that does not require I/O of large time signatures files

- Perform advanced electronics cooling analyses that can include condensation, evaporation and more, with a new printed circuit board (PCB) model that enables the import of Ansys Icepak settings
- Efficiently add, remove or replace geometry objects of your CAD model without having to re-mesh the complete model using the part replacement feature in the fault-tolerant meshing workflow
- Solve simulations more efficiently with new mesh adaption methods: Hessian error-based adaption accounts for strong and weak features and anisotropic adaption that adapts the mesh in one direction reducing the overall cell count
- Accurately predict near-wall liquid temperatures for boiling applications independent of mesh resolution
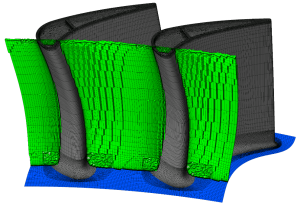
Ansys CFX and Turbo Tools
- Speed ups of more than 100X can be achieved for turbocharger turbine durability analyses using the Harmonic Analysis method in Ansys CFX
- Hybrid meshing in Ansys TurboGrid keeps a 1:1 connection between block-structured hex elements in the bulk and unstructured elements on complex features like buttons and squealer tips
- TurboGrid’s hybrid meshing technology will automate the meshing of complex turbomachinery blade designs, like inlet guide vanes (IGV) and variable guide vanes (VGV), to generate a mesh in minutes
Ansys Chemkin-Pro
- Extended the multiphase mechanism framework to include a new transient stirred reactor that supports multiphase interactions, including phase change and liquid reactions
- Improved NOx predictions using PERK mechanisms from the Model Fuel Library (MFL)
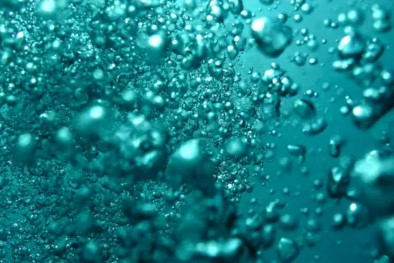

Ansys Forte
- Eulerian two-phase mixture approach to modeling liquids and two-phase mixtures enables quick and accurate simulation of liquid pumps and valves
- Extended heat-transfer model options and flexibility, including user defined functions (UDF) support
- Efficiently post process simulation results in Ansys EnSight with a new file format export option that reduces file size and loading time
Ansys Rocky
- Accelerate simulation time by reducing computation in regions with low particle interaction using the dynamic domain capability.
- Complex shaped particles can be created with a generalized particle assembly feature that enables connections of all particle types, including polyhedral, fibers, shells and more
- Enhanced coupling with Ansys Fluent now includes re-meshing, one-way transient and accounting for multi-species
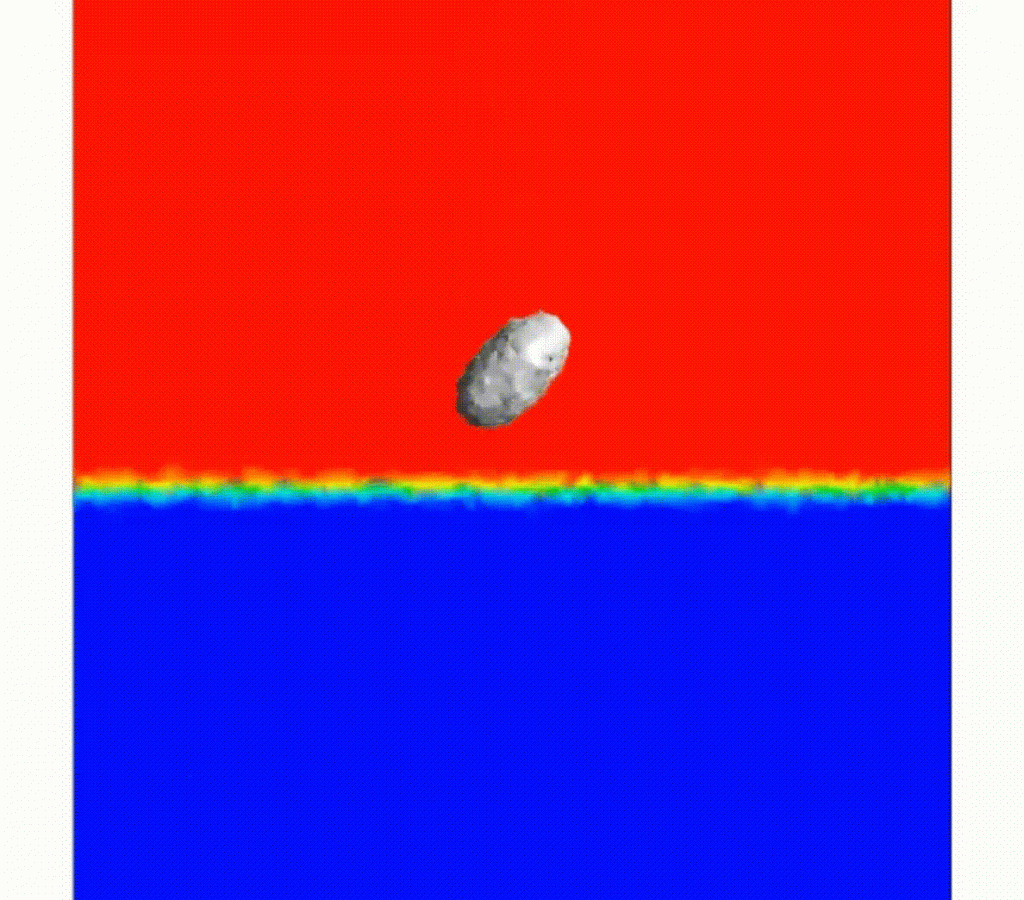
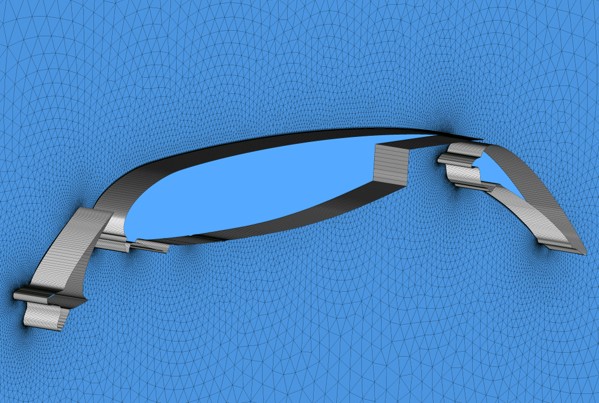
Ansys FENSAP-ICE
- Accurately predict engine icing by accounting for evaporative cooling of air by thermally coupling the air energy equation with water vapor, droplet and crystal phases
- 2D ice shape prediction calculations can be accelerated using the automated meshing workflow that produces one element thick iced grids from Ansys Fluent meshing
Ansys Ensight
- Quickly generate high-quality photo-realistic animations with the new OSPRay ray tracer engine
- Instantaneously visualize how changes to materials, lights, parts and more will look with ray traced rendering through a new preview window
All information has been prepared to the best of our knowledge. Data without guarantee.